開発・設計 豆知識
フロー・リフローの違いとは?基板実装のはんだ工程!
- 製造・組立
プリント基板に電子部品を実装する上で、電気的接続と機械的強度を確保する「はんだ付け」は極めて重要な工程です。この工程で主流となるのが「フローはんだ」と「リフローはんだ」という二つの主要な技術です。
この記事では、プリント基板実装の核心となるフローはんだとリフローはんだの違いを、原理、特徴、メリット・デメリットに至るまで徹底的に解説します。最適なはんだ付け方法の選択は、基板の品質と生産効率を大きく左右します。ぜひ、この記事を参考に、貴社の基板設計・実装戦略にお役立てください。
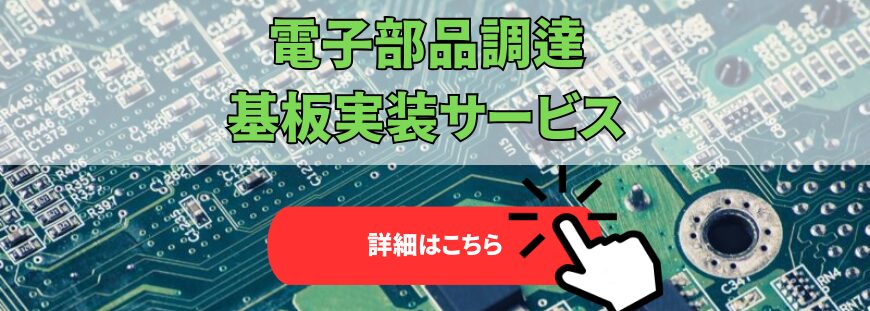
基板実装とは?
そもそも、基板実装とは、プリント基板(PCB)上に抵抗、コンデンサ、ICなどの電子部品を配置し、はんだ付けによって電気的に接続する一連のプロセスです。この工程は、スマートフォン、パソコン、自動車など、あらゆる電子機器の製造において不可欠であり、製品の性能と信頼性を決定づける重要な役割を担っています。
基板実装におけるはんだ工程
基板実装のはんだ工程は、部品と基板の導電パターンを金属である「はんだ」で接合し、電気的な接続と物理的な固定を実現します。代表的なはんだ付け方法として、以下の2つが挙げられます。
- フローはんだ(波はんだ): 溶融したはんだの波を基板裏面にあて、挿入部品の端子と基板パターンを接合。
- リフローはんだ: クリーム状のはんだを基板に塗布後、表面実装部品を配置し、加熱炉で溶融させて接合。
フローはんだとは?
フローはんだ(別名:波はんだ)は、溶融状態(液状)のはんだを満たしたはんだ槽の上を、部品実装済みの基板が一定速度で通過する際に、基板裏面から溶融はんだを波のように噴き上げ、部品の端子と基板の導電パターンを接合する技術です。主に、DIP部品などの挿入実装に用いられます。(※ちなみに、昨今ではDIP部品が減少傾向にあり、SMD部品の浸透に伴い、両面リフローの基板が増加傾向にあります。)
フローはんだの工程
- 予熱: 基板全体を均一に温め、はんだ付け時の熱衝撃を緩和し、フラックスの活性化を促進します。
- フラックス塗布: はんだの濡れ性を向上させ、酸化膜を除去するフラックスを基板裏面に塗布します。
- はんだ付け:
- 一次噴流: ノズルから勢いよく噴流するはんだの波で、部品端子の根元まで確実にはんだを供給し、未はんだを防止します。
- 二次噴流: 穏やかな噴流で、はんだの余分な付着やはんだブリッジ(不要なはんだの繋がり)を抑制し、美しいフィレット(はんだの仕上がり形状)を形成します。
- 冷却: はんだ接合部を徐々に冷却し、固化させます。
フローはんだのメリット
スルーホール部品の大量生産に非常に効率的です。比較的短時間で多くの部品をはんだ付けできます。
フローはんだのデメリット
はんだ量の調整が難しく、部品の高さや配置によっては均一なはんだ付けが難しい場合があります。はんだブリッジや未はんだ、ショートなどの不良が発生しやすい傾向があり、基板設計時に部品配置や配線パターンへの綿密な配慮が不可欠です。
リフローはんだとは?
リフローはんだは、主に表面実装部品(SMD)のはんだ付けに用いられる精密な技術です。クリーム状のはんだ(はんだペースト)を、メタルマスクと呼ばれる専用の版を用いて基板の所定箇所に正確に印刷した後、その上に電子部品を配置します。その後、リフロー炉と呼ばれる特殊な加熱炉で基板全体を精密に温度管理しながら加熱し、クリームはんだを溶融させて部品を接合します。(※現在では、SMD部品が多く、このはんだ付け方法(リフロー)が重宝されています。)
リフローはんだの工程
- クリームはんだ印刷: メタルマスクを使用して、クリームはんだを基板のランド(部品の接合部)に均一かつ正確に塗布します。
- 部品搭載: 自動実装機(マウンター)などを用いて、表面実装部品をクリームはんだの上に正確に配置します。
- リフロー加熱: 複数の温度ゾーンを持つリフロー炉内を基板が通過する間に、予熱、昇温、ピーク温度保持、冷却といった温度プロファイルに従って加熱され、クリームはんだが溶融し、部品と基板が接合されます。
- 冷却: 接合部を徐々に冷却し、はんだを固化させます。
リフローはんだのメリット
事前に正確な位置に必要な量のはんだを塗布できるため、非常に高精度なはんだ付けが可能です。はんだブリッジなどの実装不良が発生しにくく、微細な部品や高密度実装に適しています。軽量な部品であれば、基板の両面に同時に実装することも可能です。
リフローはんだのデメリット
スルーホール部品のはんだ付けには基本的に対応できません。クリームはんだ印刷には、基板パターンごとに専用のメタルマスクが必要となり、設計変更があった場合には再製作が必要となるため、初期費用やリードタイムが発生する場合があります。
フローはんだとリフローはんだの違い
フローはんだとリフローはんだの根本的な違いは、はんだを溶かすタイミングと、主に適用される電子部品の種類にあります。
- フローはんだ: 溶融したはんだを直接基板に接触させ、主にスルーホール部品の接合に用いられます。大量生産に適していますが、精度面ではリフローはんだに劣る場合があります。
- リフローはんだ: クリーム状のはんだを塗布した後、加熱して溶融させ、主に表面実装部品の接合に用いられます。高精度な実装が可能で、微細部品や高密度実装に適しています。
実際の基板実装においては、表面実装部品をリフローはんだで実装した後、スルーホール部品をフローはんだで実装するなど、両方の技術を組み合わせることも一般的です。
比較項目 | フローはんだ | リフローはんだ |
はんだの状態 | 溶融状態 | クリーム状 |
はんだ付け方法 | 溶融はんだの波を接触させる | 加熱してクリームはんだを溶融させる |
主な対象部品 | スルーホール部品(DIP部品など) | 表面実装部品(SMD) |
生産性 | 大量生産向き | 中~大量生産向き、高密度実装に適する |
精度 | 部品配置や高さに影響を受けやすい | 高精度、微細部品の実装が可能 |
不良リスク | ブリッジ、未はんだ、ショートが発生しやすい | ブリッジなどの不良が発生しにくい |
準備 | フラックス塗布 | クリームはんだ印刷、メタルマスクが必要 |
その他 | 基板全体をはんだ槽に通すため、部品への熱負荷に注意 | 局所的な加熱が難しく、基板全体の温度管理が重要 |
昨今の基板実装の進化・トレンド
昔は、基板実装といえば、挿入実装(フローはんだ)が主流でした。この理由は、そもそも市場にDIP部品しか出回っていなかったためです。一方、ある時期よりSMD部品が台頭してきました。さらに、SMD部品の実装は、DIP部品の実装と比較し、不良が起こりづらい傾向にあります。そのため、、表面実装(リフローはんだ)の活用ニーズが高まっているのです。現在では、両面リフローの基板なども多く活用されています。
基板・電子機器の開発・製造ならお任せください。
電子機器ユニット 受託開発・製造センターでは、構想設計から回路設計・基板設計・機構設計、さらには製造・試験までワンストップで対応しています。このワンストップ対応体制により、電子機器ユニットの試作・開発を丸投げできるパートナーとして幅広いお客様のご要望を解決してまいりました。 組込みボード・基板の開発・設計・製造の委託先にお悩みの皆様、是非一度当社にご相談ください。
関連する開発・設計 豆知識一覧
-
- 製造・組立
基板実装におけるはんだ不良の種類と対策
電子機器の製造に不可欠な基板実装。その品質を大きく左右するのが「はんだ付け」の工程です。…
-
- 構想設計
- 回路・基板設計
- 機構設計
- 製造・組立
ECUとは?ECUの開発・設計の委託における注意点
現代の自動車には、安全性能や快適性能、環境性能を高めるために、数多くの電子制御システムが…
-
- 製造・組立
アキシャル部品、ラジアル部品とは?それぞれの違いと実装方法を解説!
プリント基板に電子部品を実装する工程において、部品の形状とリード線の出方は実装方法を大き…
-
- 製造・組立
共晶はんだ(有鉛はんだ)と鉛フリーはんだの違いとは?それぞれの特性を解説!
プリント基板への電子部品実装において、部品同士を電気的に接続するために用いられる「はんだ…
-
- その他
- IoT機器
- 構想設計
- 回路・基板設計
- 機構設計
- 製造・組立
電子機器・IoT機器のOEM・ODMを委託する際の注意点
当記事では、電子機器・IoT機器のOEM・ODMを委託する際の注意点と題しまして、電子機…
-
- 構想設計
- 回路・基板設計
- 機構設計
- 製造・組立
電子機器ユニットの 開発/設計・製造フロー
ご存知の通り、電子機器ユニットは、現代の私たちの暮らしを支える重要な要素です。常日頃から…